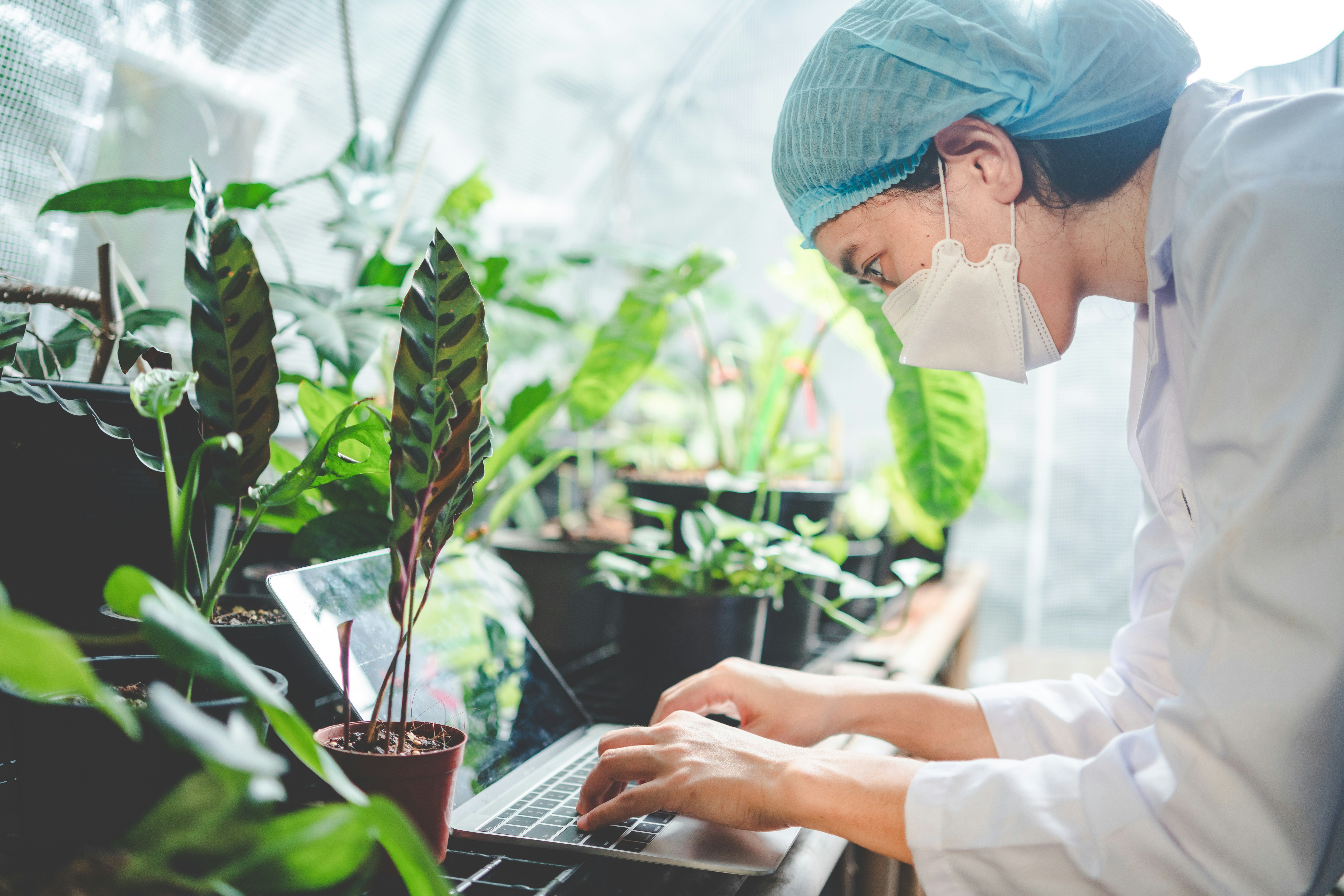
Plant efficiency is crucial for optimizing production, reducing costs, and improving the overall performance of manufacturing operations. By evaluating plant efficiency metrics, managers can identify opportunities for improvement and drive greater productivity. These metrics offer insights into how healthy resources are utilized, how much waste is produced, and how effectively plant operations meet their intended goals. This article delves into key plant efficiency metrics businesses should track to enhance operations and boost profitability.
Understanding Plant Efficiency Metrics
Plant efficiency metrics help businesses evaluate how effectively their operations are running. These metrics cover energy consumption, production rates, downtime, and maintenance. Tracking these data points allows plant managers to make informed decisions and improve processes. Efficiency is often seen as a measure of how well a plant uses resources to produce the desired output. For example, a high-efficiency score means the plant produces more goods with fewer resources.
Metrics like Overall Equipment Effectiveness (OEE) are vital for assessing the plant’s overall performance. OEE combines three key factors: availability, performance, and quality. These factors help identify areas where improvements can be made. OEE measures how healthy equipment is used in production, accounting for planned and unplanned downtime. By monitoring this metric, plants can pinpoint inefficiencies and minimize wasted time and energy.
Key Metrics for Monitoring Plant Performance
Several key metrics that plant managers should monitor to ensure optimal performance include production rate, energy consumption, downtime, and maintenance costs. Production rate refers to how many units are produced within a given time frame, clearly indicating plant throughput. A higher production rate often correlates with higher efficiency but should also be balanced with quality control measures.
Energy consumption is another essential metric. Reducing energy use while maintaining production levels can significantly reduce operating costs. Tracking energy consumption per unit of output helps identify areas for improvement. A plant that consumes excessive energy may need to invest in more efficient machinery or alter production processes to reduce consumption.
Downtime is one of the most critical factors affecting plant efficiency. Whether planned or unplanned, downtime disrupts production and causes delays. Reducing downtime is essential for improving efficiency, and this can be done by focusing on predictive maintenance and streamlining workflows. Unplanned downtime, in particular, is costly and can severely impact productivity.
Maintenance costs are another key indicator of plant efficiency. High maintenance costs may signal that equipment is aging or not adequately maintained. Regular maintenance ensures machines operate at their best, reducing the risk of breakdowns and minimizing unplanned downtime. Keeping maintenance costs under control can help boost the plant’s overall efficiency.
Improving Efficiency with OEE
OEE is one of the most widely used metrics for measuring plant efficiency. It is calculated by multiplying three components: availability, performance, and quality. Availability reflects the amount of time equipment is available for production. Performance measures how fast the equipment is running compared to its maximum speed. Quality tracks the percentage of products that meet quality standards.
To improve OEE, it’s essential to reduce downtime, optimize machine speeds, and minimize defects. Implementing a maintenance program that prevents breakdowns and addresses inefficiencies is necessary. Training employees to identify and solve problems quickly can also help maintain high OEE scores. As OEE increases, plants experience less waste, higher productivity, and more cost-effective operations.
Another aspect of improving efficiency through OEE is implementing a continuous improvement program. Plant managers can identify trends and recurring issues by regularly assessing OEE data. This helps prioritize improvements and allocate resources effectively. Over time, minor availability, performance, and quality improvements can substantially improve overall efficiency.
The Role of Automation and Technology
Automation and technology play a significant role in improving plant efficiency. Automated machinery, sensors, and data analytics allow for real-time monitoring and control of operations. Automation reduces the need for manual labor, minimizes human error, and speeds up production. As a result, plants can increase production rates without compromising quality.
Technology also allows for better data collection and analysis. Plant managers can identify patterns and predict future issues with advanced data analytics tools. For example, predictive maintenance uses data to forecast when equipment is likely to fail, allowing for proactive repairs. This reduces unplanned downtime and helps keep the plant running smoothly.
Additionally, integrating the Internet of Things (IoT) into plant operations can improve efficiency. IoT devices can monitor equipment performance, track energy consumption, and provide insights into process improvements. This data helps managers make informed decisions and optimize plant operations.
Advanced robotics is also gaining traction in many industries. Robots can perform repetitive tasks more efficiently than humans and are often used in assembly, packaging, and material handling. By automating these tasks, plants can increase their efficiency while reducing the likelihood of errors.
Driving Continuous Improvement
Achieving and maintaining high plant efficiency is an ongoing process that requires continuous improvement. Regularly reviewing performance metrics and implementing improvements can help plants stay competitive. One approach to constant improvement is adopting lean manufacturing principles. Lean focuses on eliminating waste and optimizing processes to create more value with fewer resources.
Key elements of lean manufacturing include reducing unnecessary inventory, improving process flows, and minimizing defects. These principles can be applied to all areas of plant operations, from production to maintenance to supply chain management. By continuously looking for ways to reduce waste and improve efficiency, plants can remain agile and responsive to changing market demands.
Another approach is Six Sigma, which aims to improve quality by identifying and removing the causes of defects. Six Sigma uses data-driven methods to improve processes and reduce variability, leading to higher efficiency and better-quality products.
Employee involvement is also crucial in driving continuous improvement. Engaging workers in problem-solving and decision-making can lead to valuable insights and foster a culture of efficiency. Employees empowered to identify inefficiencies and propose solutions are more likely to contribute to the plant’s success.
Tracking plant efficiency metrics is essential for any manufacturing facility that aims to stay competitive and profitable. By focusing on key metrics like OEE, energy consumption, downtime, and maintenance costs, businesses can identify areas for improvement and take action to optimize their operations. Automation and technology further enhance efficiency by streamlining processes and enabling real-time data analysis.
Achieving high plant efficiency requires a commitment to continuous improvement. Plants can drive long-term gains in productivity, quality, and profitability by adopting lean manufacturing and Six Sigma. Engaging employees in the process and fostering a culture of efficiency can also play a vital role in maintaining high performance over time. Ultimately, maximizing plant efficiency improves the bottom line and positions businesses for sustained success in an increasingly competitive marketplace.